Soleil NoirSuspension
designed by Studio Odile Decq
Soleil Noir is a poetic encounter between white and black, a symbolic struggle between light and darkness.
A suspension or ceiling lamp with an organic form in molded expanded polyurethane, whose LED source is hidden inside a disk to generate uniform indirect diffused light.
Models
D89s
Soleil Noir
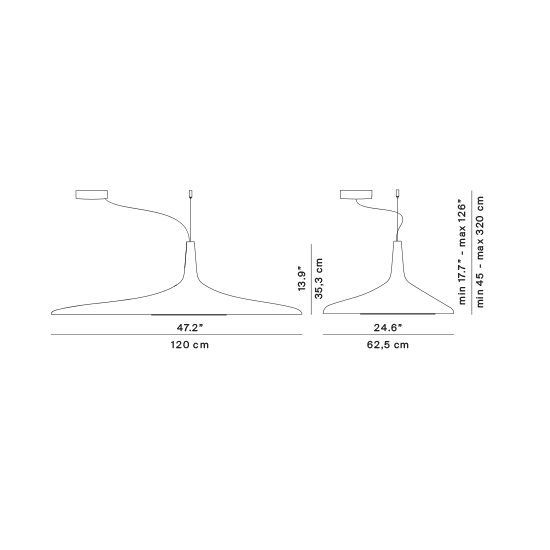
D89s
Soleil Noir
Main specifications
Typology | Suspension | ||
---|---|---|---|
Application | Indoor | ||
Material |
|
||
Finishes |
|
||
Dimensions (mm) | H 353, L 120, W 625 | ||
Weight (kg) | 6.61 | ||
Light Source | LED 35W, 3000K, CRI 80 | ||
Insulation Class | II |