GarbìWall
designed by David Dolcini
Applique that seems to take form from the wall itself, in a single solid volume of soft, regular surfaces that meet to create precise edges that become striking graphic signs. When the lamp is turned on, the light of the LED rebounds on the wall, creating a vivid contrast, and then slides inside the opening, illuminating it and delicately forming an arch on the wall.
Garbí is a lamp conceived to also function when it is off, because ambient light brings out the solid presence of its gently shaped form.
Models
D90NW
Garbì
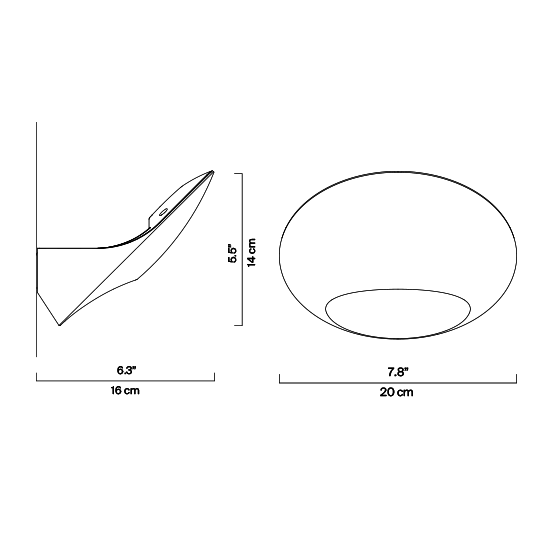
D90NW
Garbì
Main specifications
Typology | Wall | ||
---|---|---|---|
Application | Indoor | ||
Material |
|
||
Finishes |
|
||
Dimensions (mm) | H 140, L 200, W 160 | ||
Weight (kg) | 0.93 | ||
Light Source | 34W, 2700K, CRI 90 |