CostanzaTable
designed by Paolo Rizzatto
Blending tradition and technology, Costanza reinterprets a classic image in a contemporary way. The interchangeable polycarbonate lampshade emits warm, pleasant light. The sensorial dimmer rod turns the lamp on and off, alternating four light intensity levels.
D13 D13c
Costanza Telescopic – dimmer

D13 D13c
Costanza Telescopic – dimmer
Main specifications
Typology | Table | ||||
---|---|---|---|---|---|
Application | Indoor | ||||
Material |
|
||||
Finishes |
|
||||
Dimensions (mm) | H min 760 – max 1100, L base 180, W 180, D shade ø 400 | ||||
Weight (kg) | 2.03 | ||||
Light Source | LED E27 dimmable, HSGA max 105W E27 | ||||
Insulation Class | II |
D13i
Costanza Telescopic – on/off

D13i
Costanza Telescopic – on/off
Main specifications
Typology | Table | ||||
---|---|---|---|---|---|
Application | Indoor | ||||
Material |
|
||||
Finishes |
|
||||
Dimensions (mm) | H 800, L base 180, W 180, D shade ø 400 | ||||
Weight (kg) | 2.2 | ||||
Light Source | LED E27, HSGA max 105W E27 | ||||
Insulation Class | II |
D13if
Costanza Fixed – on/off

D13if
Costanza Fixed – on/off
Main specifications
Typology | Table | ||||
---|---|---|---|---|---|
Application | Indoor | ||||
Material |
|
||||
Finishes |
|
||||
Dimensions (mm) | H 800, L base 180, W 180, D shade ø 400 | ||||
Weight (kg) | 1.99 | ||||
Light Source | LED E27, HSGA max 105W E27 | ||||
Insulation Class | II |
D13pt
Costanza fixing pin – dimmer
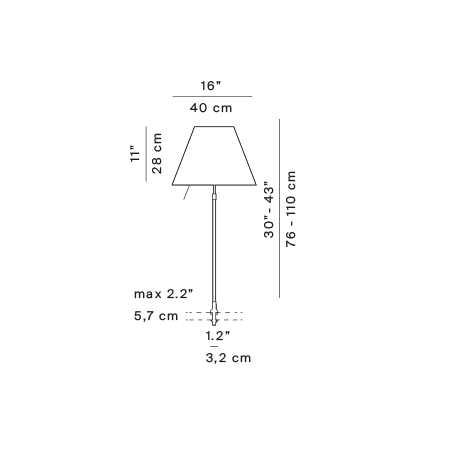
D13pt
Costanza fixing pin – dimmer
Main specifications
Typology | Table | ||||
---|---|---|---|---|---|
Application | Indoor | ||||
Material |
|
||||
Finishes |
|
||||
Dimensions (mm) | H min 760 – max 1100, D shade ø 400 | ||||
Weight (kg) | 0.54 | ||||
Light Source | LED E27 dimmable, HSGA max 105W E27 | ||||
Insulation Class | II |
D13pti
Costanza fixing pin – on/off

D13pti
Costanza fixing pin – on/off
Main specifications
Typology | Table | ||||
---|---|---|---|---|---|
Application | Indoor | ||||
Material |
|
||||
Finishes |
|
||||
Dimensions (mm) | H min 760 – max 1100, D shade ø 400 | ||||
Weight (kg) | 0.54 | ||||
Light Source | LED E27, HSGA max 105W E27 | ||||
Insulation Class | II |