Projects
Confluence
Location | Lyon, France |
---|---|
Designer | Studio Odile Decq |
Date | 2016 |
Photo credits | Roland Halbe |
Pétale by Odile Decq is a suspension luminaire concealing the magic of silence within: the body consists of a sound-absorbing panel upholstered in white fabric, improving acoustic comfort within the environment.
Products in use
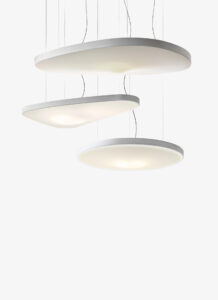
Pétale Suspension,
Designed by Studio Odile Decq