Projects
Rosenthal Wine Merchant Headquarters
Location | Brooklyn, NY |
---|---|
Client | Rosenthal Wine Merchant |
Designer | Pseudonym Studio |
Date | 2022 |
Photo credits | Shannon Dupre and Amanda Villarosa |
In 2022 Luceplan was a technical lighting partner for the project of the Rosenthal Wine Merchant offices, an American firm that is a leader in fine wine imports. For its new facility in Williamsburg, a trendy neighborhood in Brooklyn for lovers of fashion and design, the company chose the architecture studio Pseudonym. Within the project, it was necessary to create an operative space with computer workstations and a lounge area. Farel, thanks to its decorative and technical characteristics, has become the perfect solution in this context: it reduces sound reverberation while adding a lively touch of color to the setting, ensuring excellent technical lighting performance at the same time. Also in collaboration with Luceplan, the kitchen area features the Lita ceiling lamp designed by David Dolcini, with its characteristic opaline blown glass diffuser that works perfectly with the structure of the building.
Products in use
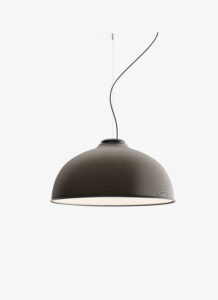
Farel Suspension,
Designed by Diego Sferrazza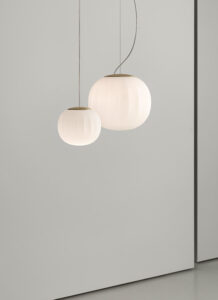
Lita Suspension,
Designed by David Dolcini