Projects
Bergen Academy of Art & Design
Location | Bergen, Norway |
---|---|
Designer | Scenario interiørarkitekter MNIL |
Date | 2018 |
Photo credits | GATIS ROZENFELDS |
Intimate and conceptual, Ascent by Daniel Rybakken is a light packed into a small format with surprising potential for varying and creating a light setting perfectly tailored to the situation. It offers the user a refined treatment of artificial light, allowing for personalization of light flow by raising or lowering the shade and eliminating the use of a conventional light switch.
Products in use
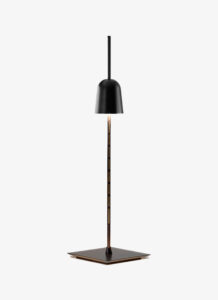
Ascent Table,
Designed by Daniel Rybakken