Designers
Archirivolto


1/2
2/2
Archirivolto Design was born in 1983 in Colle di Val d’Elsa, in the province of Siena, thanks to the collaboration between Marco Pocci and Claudio Dondoli.
Specializing in the design of furnishing accessories, with a history of thirty years, Archirivolto is in contact with any type of technology and material, especially plastic, gaining experience on anything that can be produced or printed.
A project that flies high the signature of Made in Italy through numerous collaborations with internationallybrands, stands out in particular in the home & luxury design and contract.
Related products
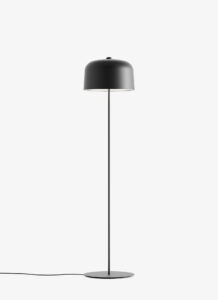
Zile Floor,
Designed by Archirivolto
Zile Suspension,
Designed by Archirivolto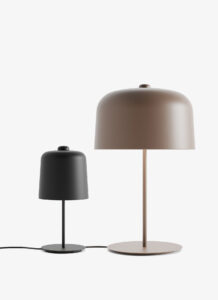
Zile Table,
Designed by Archirivolto