Designers
Riccardo Sarfatti
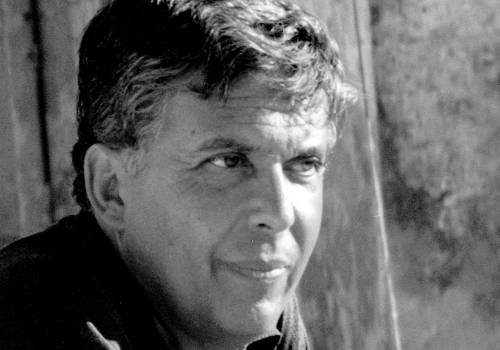
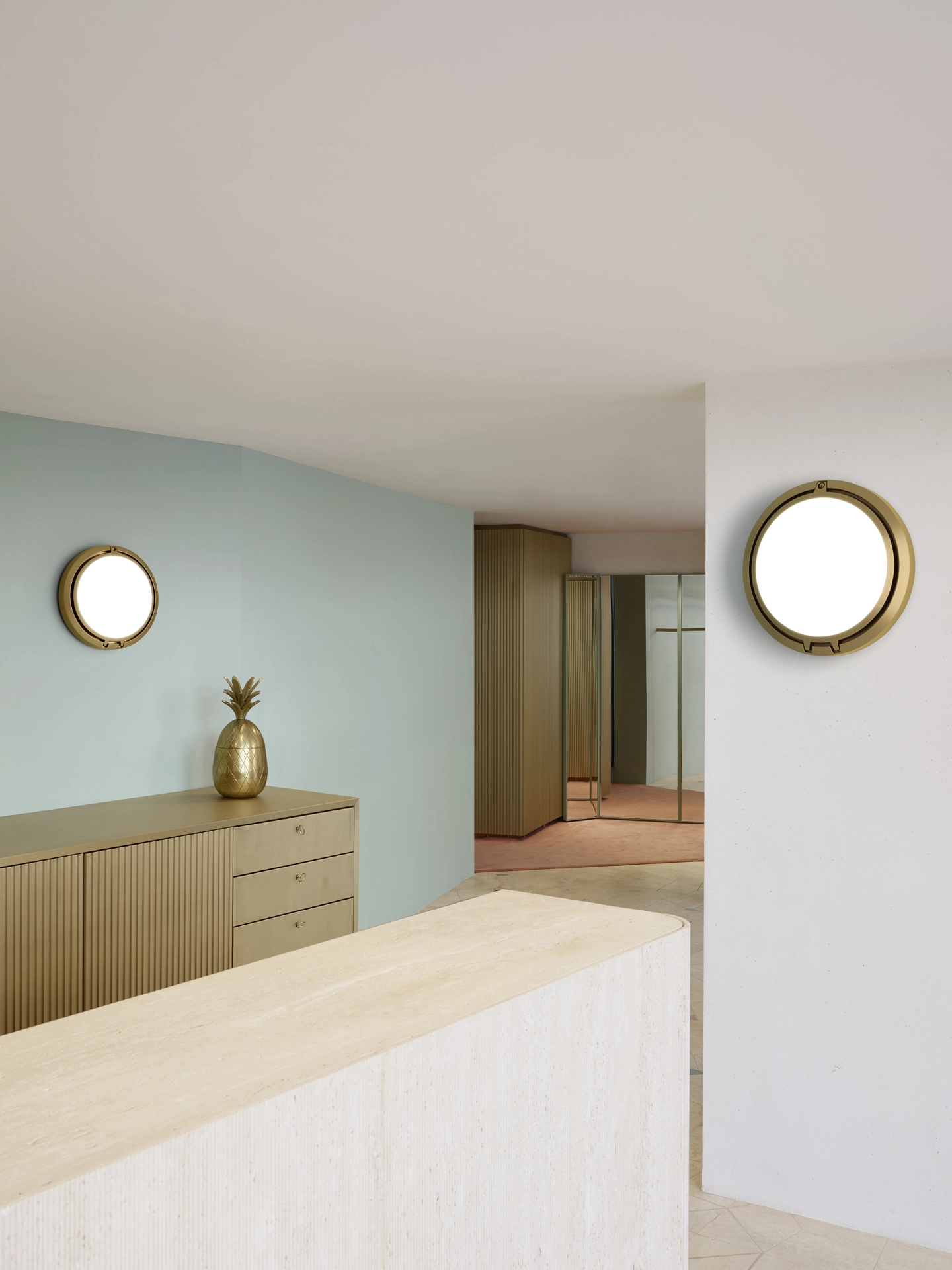
1/2
2/2
(Milan, 3 April 1940 – Tremezzo, 10 September 2010) Graduated in Architecture in 1965 from Milan Polytechnic, he became assistant lecturer in Town Planning and Acting Professor of History of Architecture at Venice and at Milan.
He was the son of Gino Sarfatti, Arteluce’s founder and one of the pioneers of Italian design as regards lighting. Alongside his university work, Riccardo Sarfatti worked at Arteluce from 1964 to 1978.
In 1979, together with Paolo Rizzatto and Sandra Severi, he founded Luceplan, of which he was Managing Director and General Manager until 2004. He was the Chairman of companies linked to Luceplan, operating in various geographical areas, in the production and distribution fields.
He wrote numerous articles and essays that were published in specialist reviews and gave lectures on themes of design and lighting in conferences and debates all over the world.
From 1997 to 2002 he was Chairman of Assoluce, the Italian association of producers of lighting appliances, and Vice-Chairman of Federlegno-Arredo; in this capacity he represented Italy in the CELMA (the European Lighting Manufacturers’ Association). He was Chairman of CNAD (National Council of Associations for Design). He promoted the website www.imprenditoriliberal.it, and was a member of the Presidential Committee for Liberty and Justice and of the National Committee of the Lista Prodi. He stood as a candidate for the position of Chairman in the Lombardy Regional elections in 2005 and since then was active in politics as a Regional Councillor.
Related products
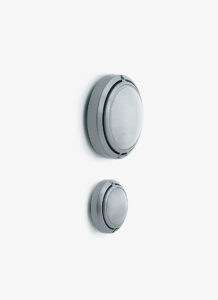
Metropoli Ceiling Wall,
Designed by Alberto Meda, Paolo Rizzatto, Riccardo Sarfatti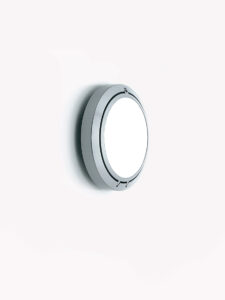
Metropoli outdoor Ceiling Wall,
Designed by Alberto Meda, Paolo Rizzatto, Riccardo Sarfatti