News ed eventi
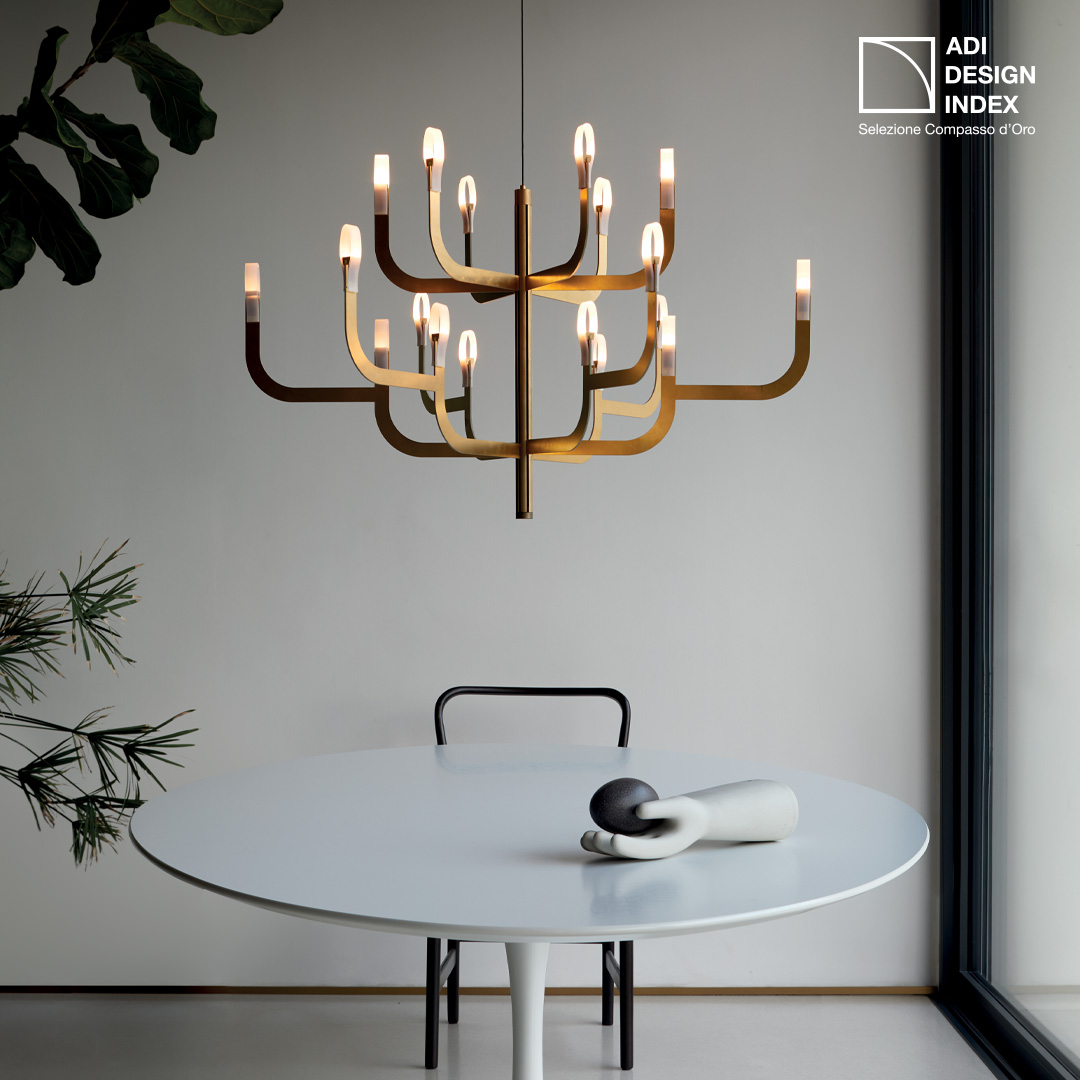
Ottobre 31, 2024
Selezione ADI Design Index 2024 per J-us
J-us, nata dal design di Alessandro Zambelli, è una vera e propria metamorfosi del tradizionale chandelier a bracci, definizione che le è valsa la selezione da parte dell’Osservatorio permanente del Design ADI per la pubblicazione sull’ADI Design Index 2024, riconoscimento che permetterà di concorrere per il Premio Compasso d’Oro 2026.
Innovativa nella sua tecnologia e versatile nell’aspetto più formale, J-us rivisita il concept del tradizionale lampadario e lo reinterpreta in chiave contemporanea.
Elementi quali innovazione, ricerca dei materiali e nuove soluzioni per la conduzione dell’elettricità, concorrono a creare un oggetto sofisticato in grado di sciogliere la complessità tecnologica in linee pulite e di grande impatto visivo, qualità che hanno condotto Luceplan ad un altro importante risultato.
Story correlata