Grande Costanza Open AirSospensione
designed by Paolo Rizzatto
The Grande Costanza Open Air suspension lamp, thanks to its enveloping glow and timeless classic design, adds a touch of elegance and refinement to outdoor spaces like terraces and gazebos, fitting perfectly into both public and private contexts. The suspension version has a thin polycarbonate diffuser (diameter 50 and 70 cm), and an IP65 optical housing connected to the shade by three small rods.
D13GSO – 50
Grande Costanza Open Air paralume ø 50
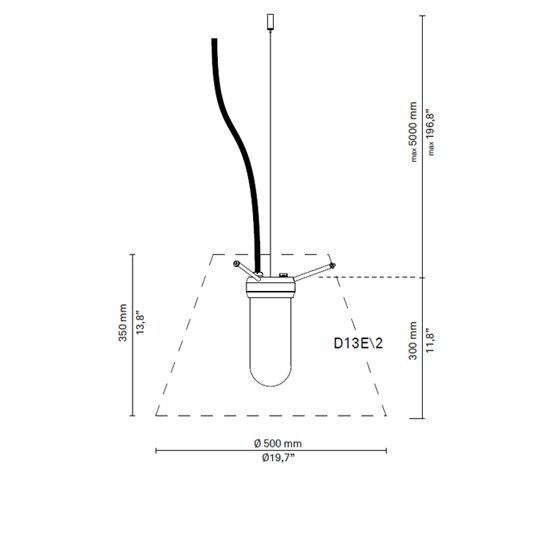
D13GSO – 50
Grande Costanza Open Air paralume ø 50
Specifiche principali
Typology | Sospensione | ||||
---|---|---|---|---|---|
Application | Esterno | ||||
Material |
|
||||
Finishes |
|
||||
Dimensions (mm) | H max 5000, D shade ø 500 – h 350 | ||||
Weight (kg) | 1.75 | ||||
Light Source | max 15W | LED E27 | ||||
Insulation Class | I |
D13GSO
Grande Costanza Open Air paralume ø 70

D13GSO
Grande Costanza Open Air paralume ø 70
Specifiche principali
Typology | Sospensione | ||||
---|---|---|---|---|---|
Application | Esterno | ||||
Material |
|
||||
Finishes |
|
||||
Dimensions (mm) | H max 5000, D shade ø 700 – h 490 | ||||
Weight (kg) | 2.2 | ||||
Light Source | max 15W | LED E27 | ||||
Insulation Class | I |