FarelSospensione
designed by Diego Sferrazza
Farel introduce per la prima volta nel catalogo Luceplan l’iconica struttura a cupola, una geometria neutra proposta in materiale termoformato fonoassorbente rivestito di tessuto all’esterno. È possibile personalizzare la lampada grazie a una combinazione di colori del paralume che spaziano da tonalità fredde, calde e neutre per l’esterno, abbinate a toni scuri o chiari per l’interno.
Farel è una lampada a bassissimo impatto ambientale. Il tessuto che riveste esternamente il paralume proviene da filati riciclati al 100%. Luceplan ha sposato l’iniziativa SEAQUAL, un progetto su vasta scala di pulitura dei mari e delle zone costiere dai rifiuti plastici, al fine di trasformarli in materiale grezzo riciclato completamente tracciabile.
Anche il feltro, che riveste l’interno del paralume, è costituito da materiale riciclato al 60%.
D96/6DW D96/6D
Farel ottica LED

D96/6DW D96/6D
Farel ottica LED
Specifiche principali
Typology | Sospensione | ||||||
---|---|---|---|---|---|---|---|
Application | Interno | ||||||
Material |
|
||||||
Finishes |
|
||||||
Dimensions (mm) | H 45 | ||||||
Weight (kg) | 1.2 | ||||||
Light Source | 23W, 2700K, 3000K, CRI 90 | ||||||
Insulation Class | I |
D96/1EB D96/1EN
Farel ottica E27

D96/1EB D96/1EN
Farel ottica E27
Specifiche principali
Typology | Sospensione | ||||||
---|---|---|---|---|---|---|---|
Application | Interno | ||||||
Material |
|
||||||
Finishes |
|
||||||
Dimensions (mm) | H 30 | ||||||
Weight (kg) | 0.7 | ||||||
Light Source | MAX 70W | ||||||
Insulation Class | I |
Get Inspired
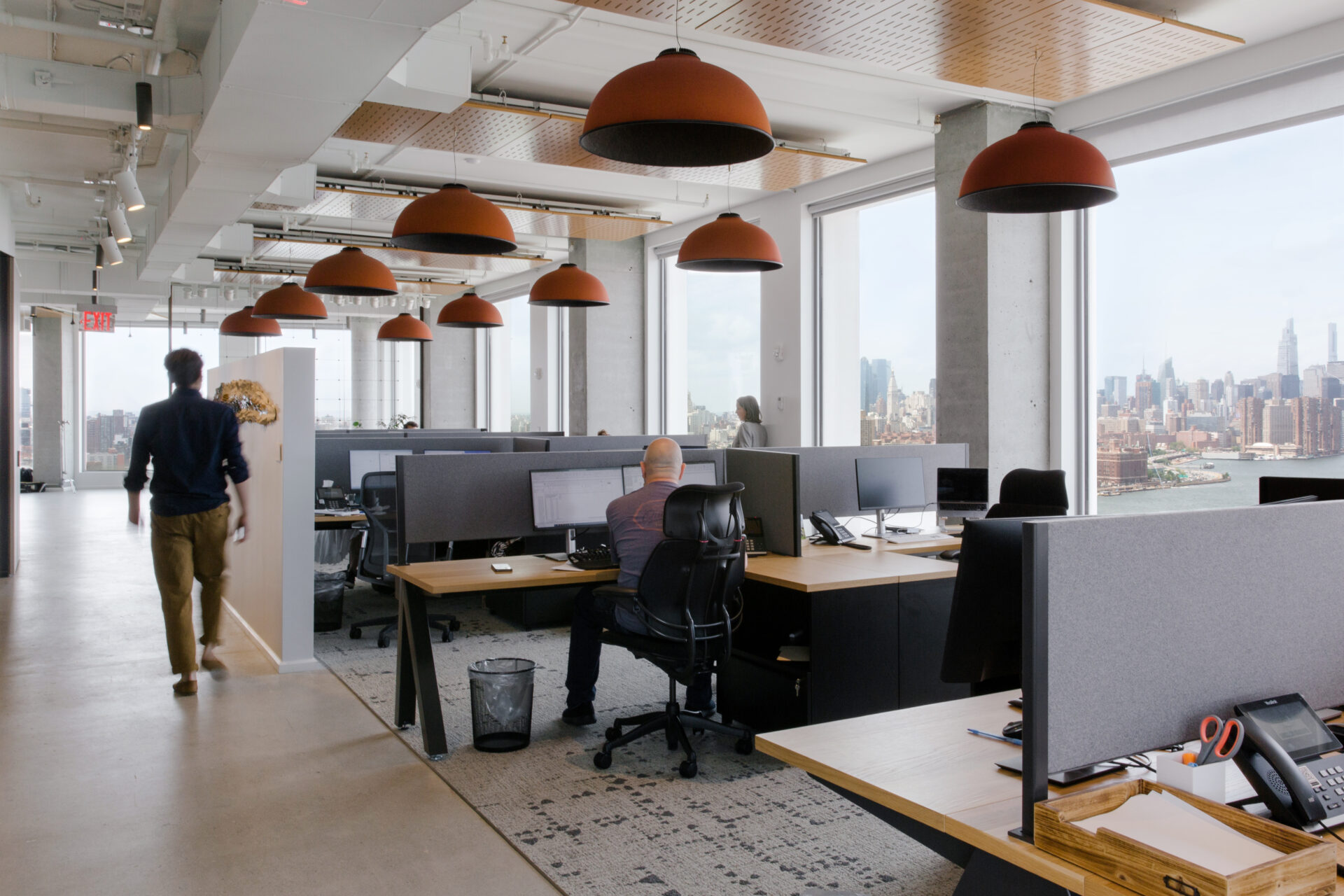
Nel 2022 Luceplan è stato partner illuminotecnico anche per il progetto di uffici Rosenthal Wine Merchant, azienda americana leader nell’importazione di vini pregiati. Per la sua nuova sede a Williamsburg, quartiere di tendenza a Brooklyn per gli amanti della moda e del design, lo studio di architettura ha scelto Farel, come soluzione perfetta in questo contesto.
Offriamo le soluzioni per ogni spazio, sia per ambienti pubblici o privati. Scopri le nostre referenze e lasciati ispirare.
Projects