BulbulliaSoffitto Parete
designed by Francisco Gomez Paz
Una serie di parabole di varie dimensioni s’intersecano generando la caratteristica geometria delle bolle di sapone; si tratta di forme coniche, ampie e piatte, ognuna delle quali è costituita da una sagoma in policarbonato bianco che, piegandosi leggermente, assume una natura strutturale. Alcentro di ciascuna bolla si accende la sorgente luminosa: essa racchiude l’anima della lampada e diffonde, grazie ai LED integrati dimmerabili, una luce gradevole e morbida che si riflette verso l’interno del cono.
D95A3
Bulbullia 3 corpi

D95A3
Bulbullia 3 corpi
Specifiche principali
Typology | Soffitto, Parete | ||
---|---|---|---|
Application | Interno | ||
Material |
|
||
Finishes |
|
||
Dimensions (mm) | H 370, L 310, W 70 | ||
Weight (kg) | 0.75 | ||
Light Source | LED 17 W , 2700K, CRI 90 | ||
Insulation Class | II |
D95A5
Bulbullia 5 corpi

D95A5
Bulbullia 5 corpi
Specifiche principali
Typology | Soffitto, Parete | ||||
---|---|---|---|---|---|
Application | Interno | ||||
Material |
|
||||
Finishes |
|
||||
Dimensions (mm) | H 620, L 370, W 70 | ||||
Weight (kg) | 1.28 | ||||
Light Source | LED 27 W, 2700K, CRI 90 | ||||
Insulation Class | II |

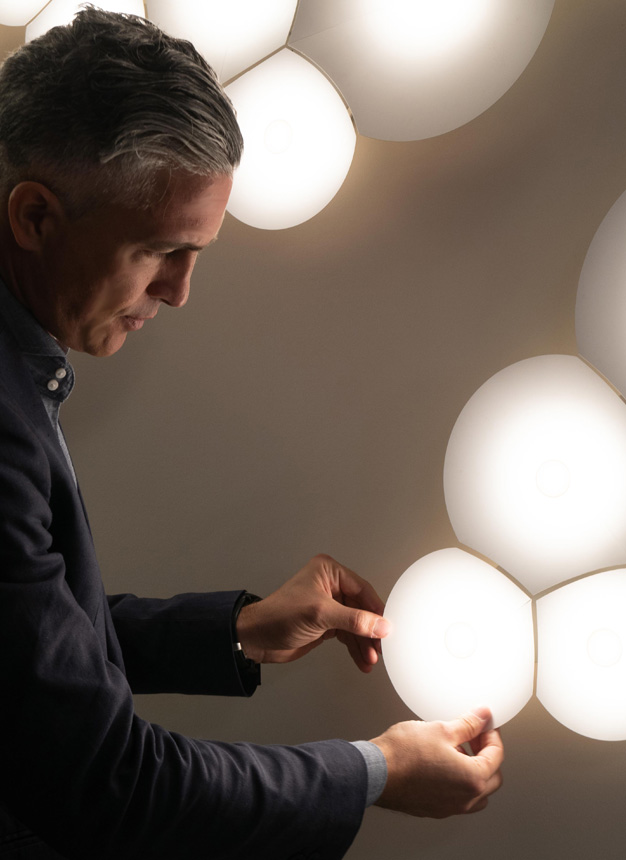
Bulbullia ha la possibilità di creare grandi configurazioni, grazie a un giunto meccanico ed elettrico che collega le lampade.