BereniceTerra
designed by Alberto Meda, Paolo Rizzatto
Leggera ed equilibrata, consente di posizionare il punto luce vicino a ciò che si desidera illuminare. Il riflettore parabolico, in alluminio o vetro pressato, emette un fascio luminoso direzionato adatto alla lettura.
D12NT
Berenice
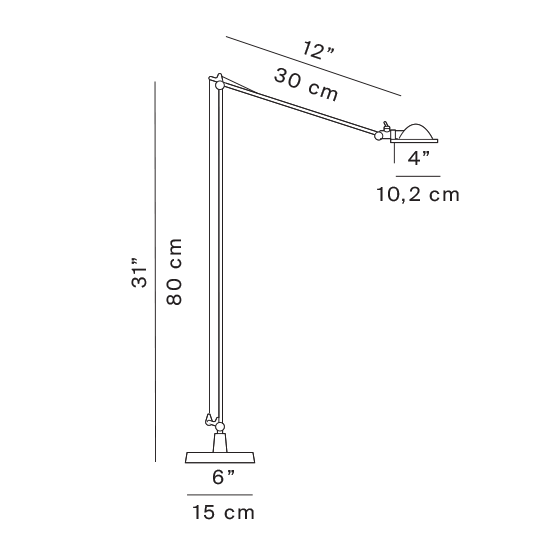
D12NT
Berenice
Specifiche principali
Typology | Terra | ||||
---|---|---|---|---|---|
Application | Interno | ||||
Material |
|
||||
Finishes |
|
||||
Dimensions (mm) | H 800 arm base, L 300 arm head, D head Ø 102, base Ø 150 | ||||
Weight (kg) | 3.2 | ||||
Light Source | LED 2W G4 3000K (supplied); HSGST max 10W G4/GY 6.35 12V; max 12.6 x 36 mm , 3000K, CRI 80 | ||||
Insulation Class | III |