Designers
Diego Sferrazza


1/2
2/2
Nato il 9 ottobre 1976 a Sassari, vive e lavora a Milano, dove ha frequentato Storia dell’Arte all’Università Statale di Milano. Ha iniziato a lavorare come industrial designer dal 2000, collaborando con alcuni studi e show-room.
I suoi progetti sono stati presentati in molte mostre internazionali come il Salone Satellite, il Salone del Mobile, l’IDA di Amsterdam, l’YDM di Berlino, Light and Building di Francoforte, ecc. Lavora anche come consulente freelance per progetti di lighting design e come designer di mostre.
Dal 2006 sviluppa progetti per molte aziende come Ligne Roset, Gotha, Gruppo-Sintesi, Haribo, Orange Network, Sphaus, Tecnodelta.
Prodotti correlati
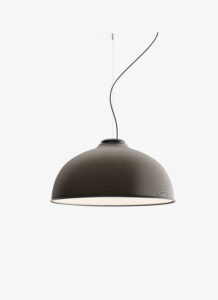
Farel Sospensione,
Designed by Diego Sferrazza