News and events
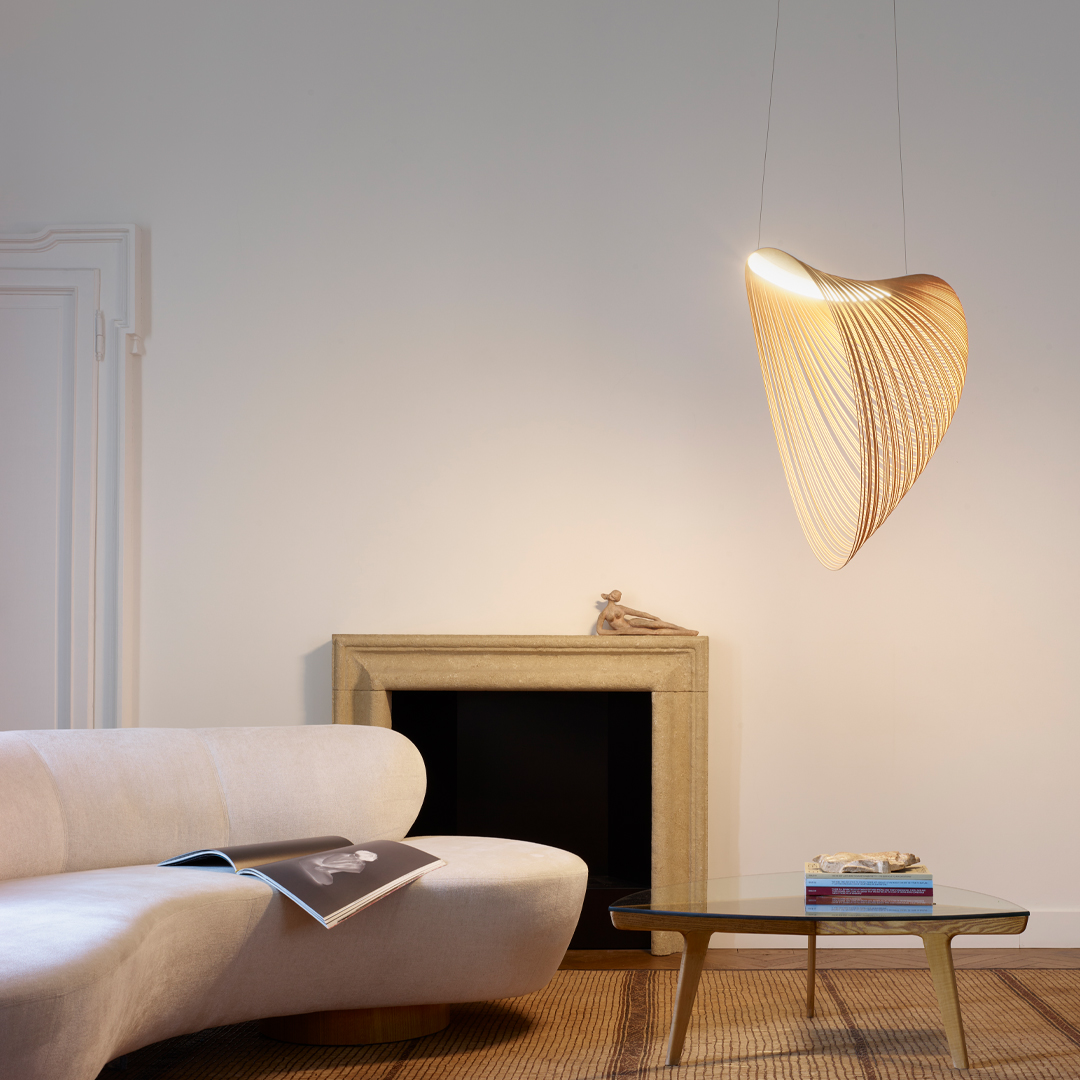
December 11, 2023
The editorial team of LIVING has chosen ILLAN as one of the design icons of the last 10 years
“Living.corriere.it – the website of the monthly Living supplement of Corriere della Sera, which also reaches readers of this leading daily newspaper through online channels – has set aside an entire section for the 10th anniversary of the magazine created by RCS in 2013 and directed by Francesca Taroni. The monthly magazine is very popular, not only in Italy but also on an international level. The editorial staff, known for its rigorous selection of the most innovative products worthy of note, has chosen Illan – designed by Zsuzsanna Horvath for Luceplan in 2019 – as one of the design icons of the last 10 years.
A product with a light, flexible design, where the body of the lamp is obtained from plywood cut with lasers along dense, equidistant lines. When suspended from the ceiling, Illan takes on volume thanks to the force of gravity, assuming its characteristic form that floats in the air. The strong decorative and emotional impact, expressed through an intelligent and original use of the materials, makes this lamp a truly special design icon.”