News and events
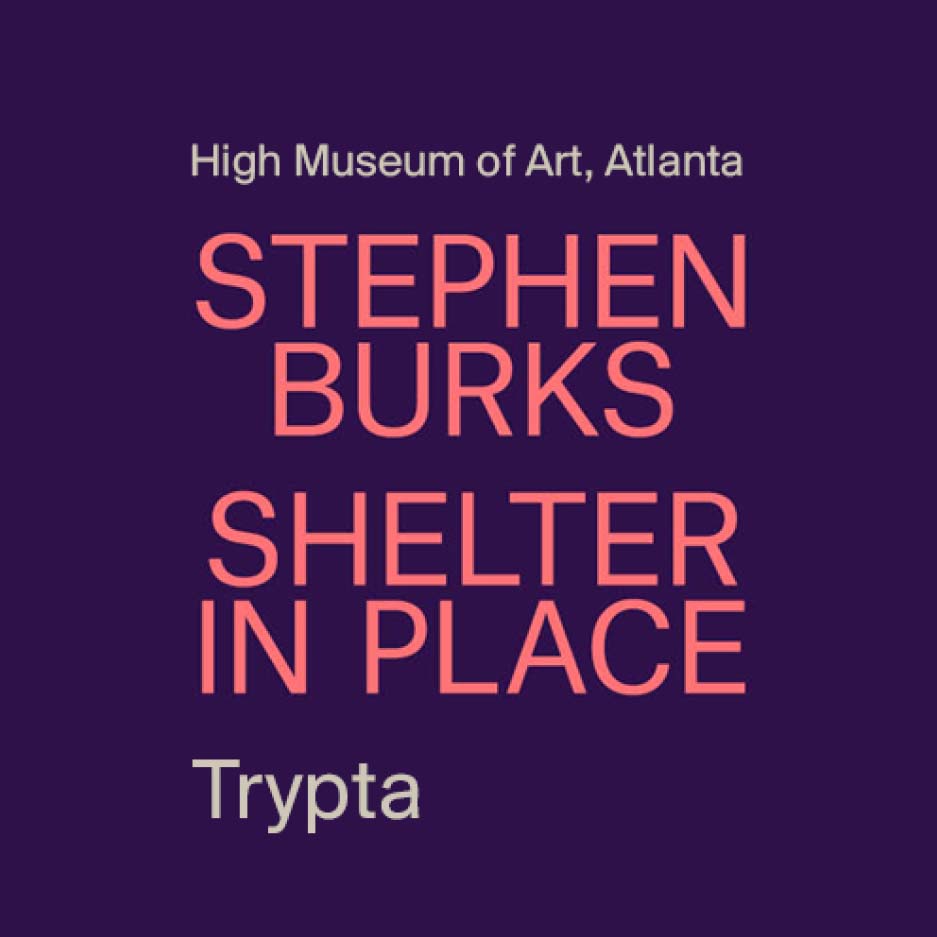
September 23, 2022
Trypta designed by Stephen Burks, takes the stage at the High Museum of Art in Atlanta
On 16 September 2022, the High Museum of Art in Atlanta unveiled Shelter in Place, an exhibition on the African-American designer Stephen Burks. Until 5 March 2023, visitors can see an overview of his most important works of the last ten years, together with a new project on the design of the future. The exhibition underscores Burks’ holistic approach, moving through the disciplines of art, architecture and design to find points of contact.
Among the projects on display, Trypta is the suspension lamp designed by Stephen Burks for Luceplan in 2018, which combines acoustic comfort with outstanding technical lighting performance, in a range of different sizes and colors.With its high sound-absorbing efficiency, Trypta is a true architectural feature capable of characterizing and personalizing spaces. Its decorative impact relies on panels covered in flame-retardant knit fabric, giving the lamp a unique personality.