KoinèTrack system
designed by Mandalaki Studio
Connected to the slim track by means of a practical adaptor and a simple action, Koinè suspension lamp meets with a new application in a growing number of possible configurations. The compatible model is the suspension version diameter 20cm.
The overall luminous effect of the Koinè project prevents glare, ensuring a high level of visual comfort. The light beam distributed by the lens is homogenous and distinct, a broad cone of light with clearly-defined edges.

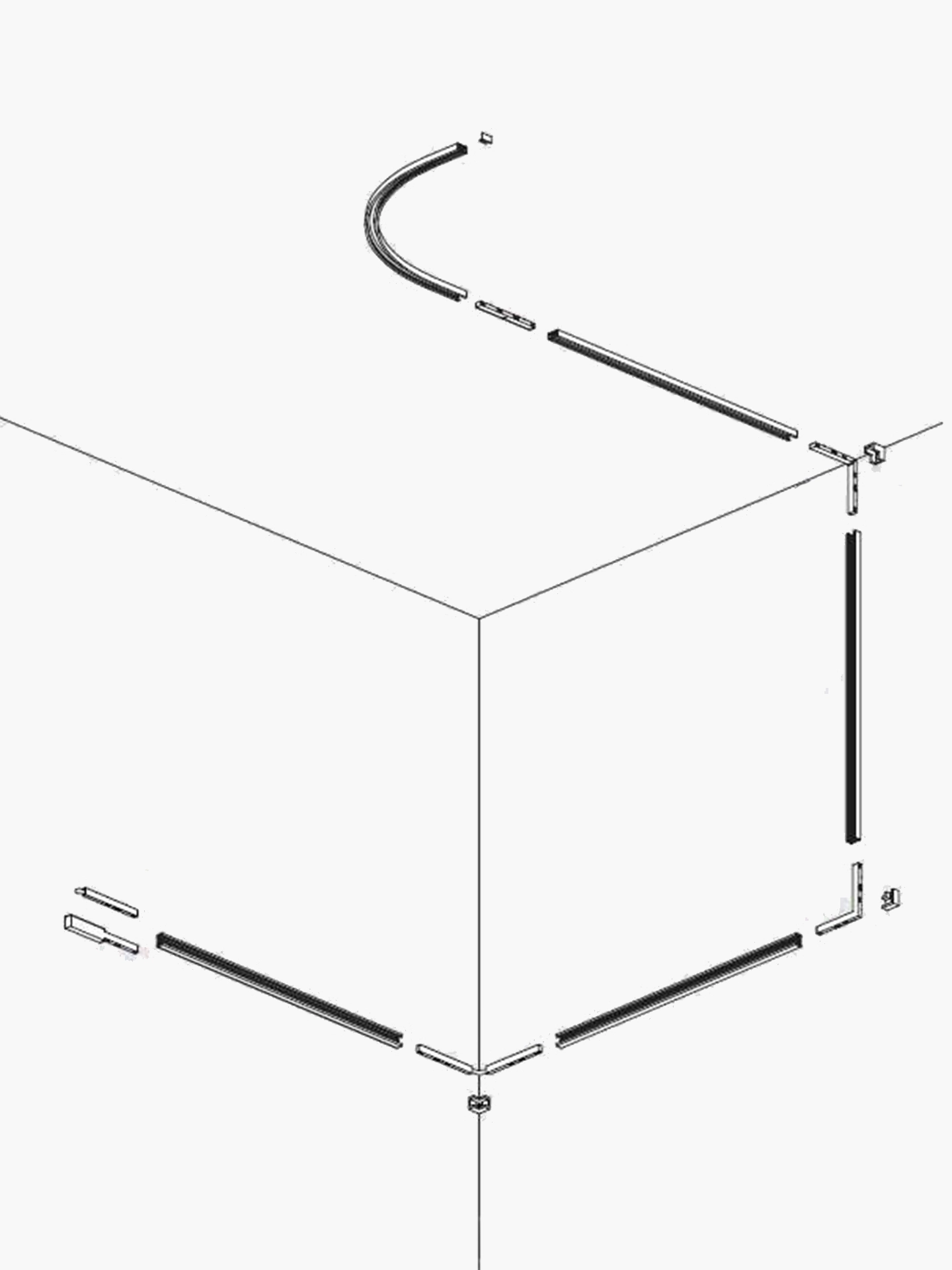
Elegant and essential, with its infinite possibilities and three types – ceiling/wall, built-in and suspension – the new track system is the ideal solution for projects in residential contexts and contract applications.
Discover the track solution and the possible combinations suitable for your projects
Lighting systems