News and events
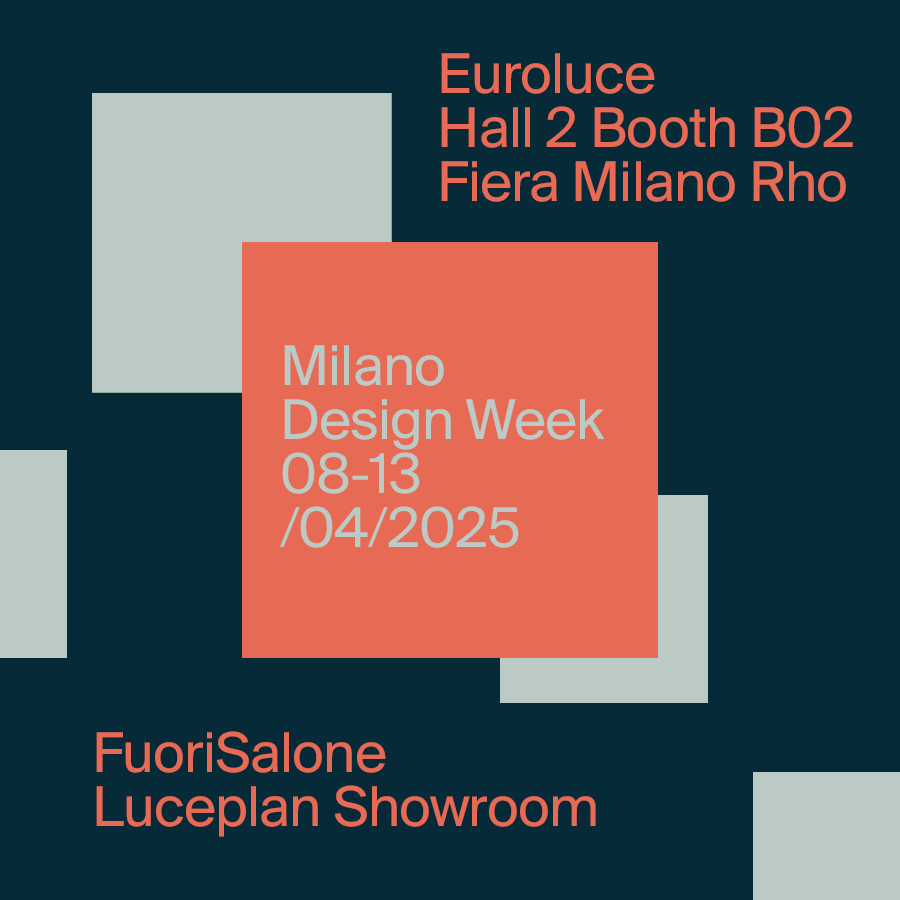
February 24, 2025
Luceplan at Milan Design Week 2025
New collections and range extensions always in the sign of lighting innovation. Projects by Studio Odile Decq, Mandalaki, Daniel Rybakken, Umut Yamac and Alessandro Zambelli.
Milan Design Week 8-13/04/2025
Euroluce – hall 2 – booth B02
Fuorisalone – corso Monforte 7, Milano