Soluzioni acustiche

Assaporare il benessere acustico
BENEFICI DEL COMFORT ACUSTICO E ILLUMINOTECNICO
Negli spazi collettivi – dedicati al lavoro, allo studio, alla ristorazione, al tempo libero – l’inquinamento acustico causato da un’eccessiva propagazione di rumori e suoni molesti, rischia di incidere negativamente sull’equilibrio psicofisico dell’uomo. Anche l’illuminazione influisce sul nostro benessere e svolge un ruolo fondamentale nella creazione di uno spazio adeguato alle varie esigenze. Fornire un’illuminazione adeguata e allo stesso tempo una maggiore qualità acustica – una migliore qualità del parlato e una riduzione della propagazione del suono – permette di realizzare un ambiente confortevole, contribuendo al miglioramento del benessere e della produttività.
L’ESPERIENZA DI LUCEPLAN
Dal 2012 Luceplan vanta una consolidata esperienza in soluzioni “all-in-one” che combinano alte prestazioni illuminotecniche, elevate prestazioni di fono-assorbenza e un design di alto livello per ogni ambiente.
Progettiamo per i nostri sensi

Alte prestazioni per l’assorbimento acustico
I materiali utilizzati per le lampade acustiche garantiscono un elevato assorbimento acustico e diminuiscono il rimbombo sonoro, in particolare collegato alla voce umana che ha un range di frequenza che varia tra 200 e 3000 Herts (Hz).
Eccezionale resa luminosa
Crediamo che una buona illuminazione sia importante e una necessità a cui non si può prescindere. I nostri apparecchi di illuminazione fonoassorbenti sono certificati per garantire un minimo di +4000 lumen con un basso abbagliamento
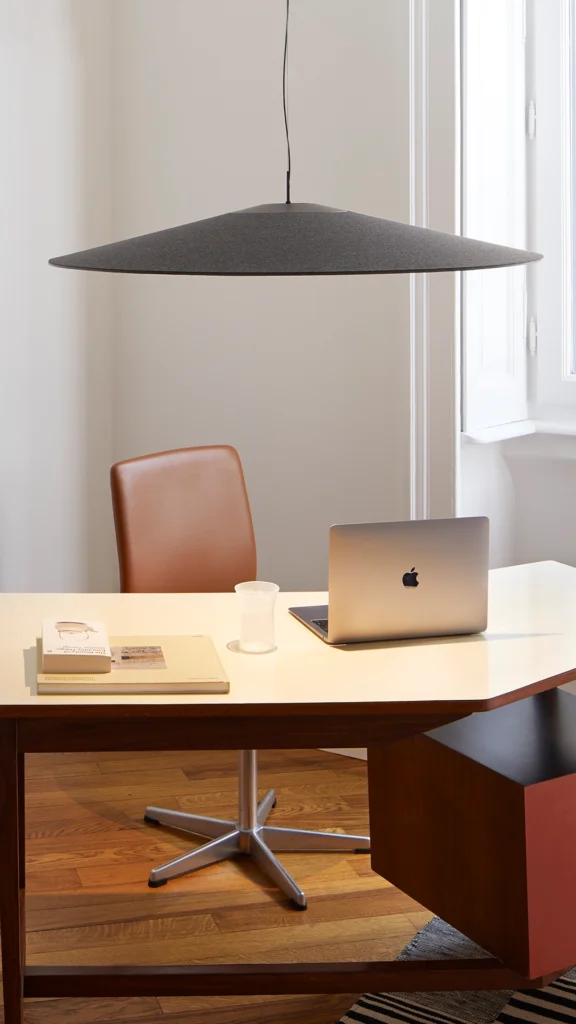
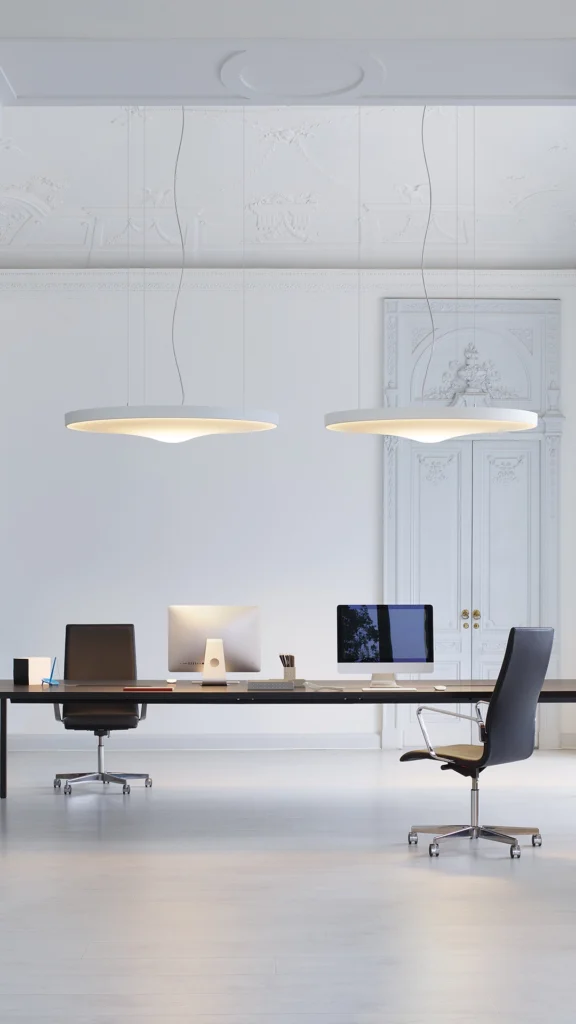
Design di alta qualità
Una serie di prodotti che sono veri e propri elementi architettonici capaci di definire e personalizzare gli ambienti. I nostri prodotti altamente performanti sono frutto della collaborazione tra ingegneri e architetti di fama mondiale come Odile Decq e Monica Armani, nonché i designer Diego Sferazza e Stephen Burks.
L’esperienza con i nostri prodotti
L’esperienza di Silenzio nel progetto di Charlottehaven hotel in Copenhagen, raccontato da Lars Pontoppidan, General Manager.
Scopri le nostre soluzioni
I nostri prodotti sono sistemi di illuminazione che abbinano soluzioni d’arredo e comfort acustico per spazi pubblici e privati, risposte progettuali di grandi capacità prestazionali che accompagnano la bellezza del disegno alla qualità della luce: un’illuminazione sartoriale che arreda e personalizza l’ambiente, perfetta espressione del binomio tecnologia e design.
Scopri la soluzione più adatta al tuo contesto e lasciati ispirare dai nostri progetti.
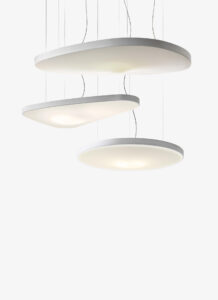
Pétale Sospensione,
Designed by Studio Odile Decq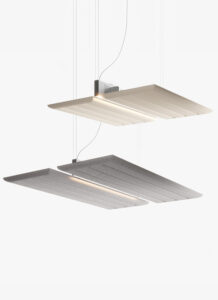
Diade Sospensione,
Designed by Monica Armani
Farel Sospensione,
Designed by Diego Sferrazza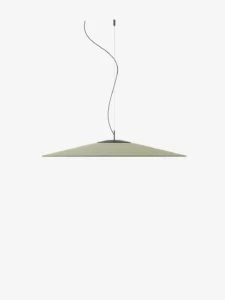
Koinè acoustic Sospensione,
Designed by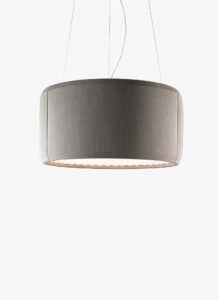
Silenzio Sospensione,
Designed by Monica Armani
Trypta Sospensione,
Designed by Stephen BurksPétale. L’eleganza del silenzio
Silenzio. L’illuminazione sartoriale


Silenzio Sospensione,
Designed by Monica ArmaniI materiali utilizzati in Silenzio garantiscono l’assorbimento del suono e impediscono la sovrapposizione acustica, in particolare nel caso del parlato umano, che si colloca nella gamma di frequenze tra 200 e oltre 3000 hert (Hz).
Farel. Design iconico per il comfort acustico
Koinè. Eleganza per nuovi scenari luminosi e acustici

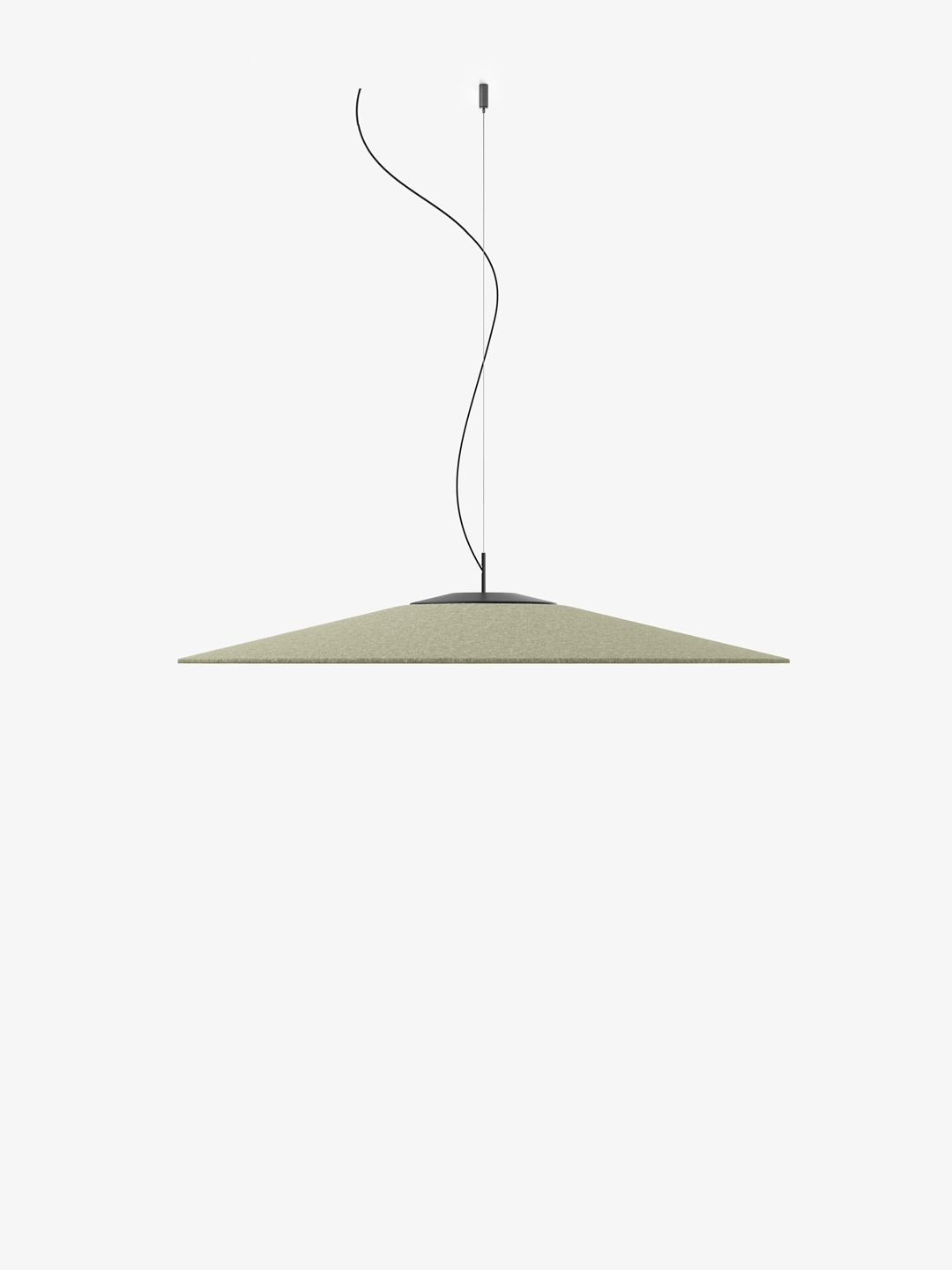
Koinè acoustic Sospensione,
Designed by Mandalaki StudioAll’alta performance tecnologica ed illuminotecnica che la contraddistingue, Koinè nella versione fonoassorbente, aggiunge un’ulteriore componente
innovativa. Il riflettore diventa un cappello in feltro riciclato al 60% che, oltre ad avere un importante ruolo decorativo, permette di migliorare il comfort acustico nello spazio diminuendo i tempi di riverbero del suono.
Diade. The wings of silence


Diade Sospensione,
Designed by Monica ArmaniI due pannelli “ali” possono essere posizionati verticali o orizzontali a creare una quinta o un grande plafone. Le due soluzioni proposte risolvono in un unicum luce, fono-assorbenza e il “ceiling” dello spazio, eliminando la necessità di controsoffittare.

Trypta. Il sistema illuminotecnico per il comfort acustico



Trypta Sospensione,
Designed by Stephen BurksTrypta è un sistema di lampade a sospensione che offre una combinazione di caratteristiche acustiche e prestazioni illuminotecniche in diverse dimensioni e colori. Il corpo cilindrico in alluminio è dotato di due sorgenti LED per un’emissione di luce sia diretta che indiretta e diffusa.
Lavoriamo insieme al tuo progetto
Luceplan non è solo prodotto, ma anche servizio: il valore aggiunto della collaborazione con l’azienda si basa sull’interazione con architetti e interior designer, che si affidano al supporto di un esperto team interno di lighting designer e tecnici. Contattaci per una consulenza acustica e illuminotecnica del tuo progetto.